Machines used in the crushing and screening plant where construction and demolition wastes are crushed; UMA110 mobile primary feeding and crushing unit, SMK1115 mobile secondary impact crusher unit, UME2060x3 mobile inclined screen unit and belt conveyors are fixed.
UMK series 110 mobile jaw crusher was used as the primary crusher in the facility. The bunker volume of the mobile primary feeding unit is 30 m³ and it has a vibrating feeder with dimensions of 1200 x 5000 mm. There is a double-stage grid system to separate the grounded and fine material. When necessary, a clapper groove is made to add or remove from the system. Jaw crushers, which are designed to crush materials of any hardness, ensure that the material is compressed and broken between two movable and fixed jaws. The fixed jaw and the movable jaw, moved by an eccentric shaft, are located in such a way that they form a V-shaped narrowing angle between them. The material is grasped by the elliptical movement and breaks down due to the pressure exerted by the two jaws. This process repeats until the material reaches the desired size. Since the outlet opening is adjustable between 100 – 250 mm, it allows different sizes of materials to be obtained. Jaw crushers are high capacity and long-lasting against wear and easy to maintain.
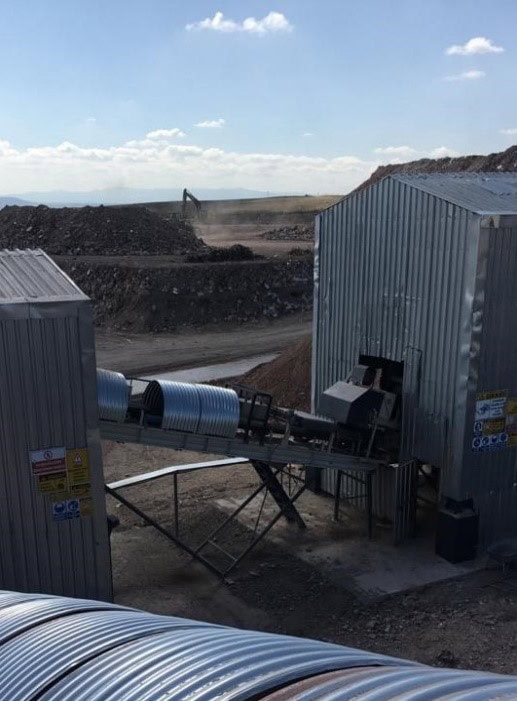
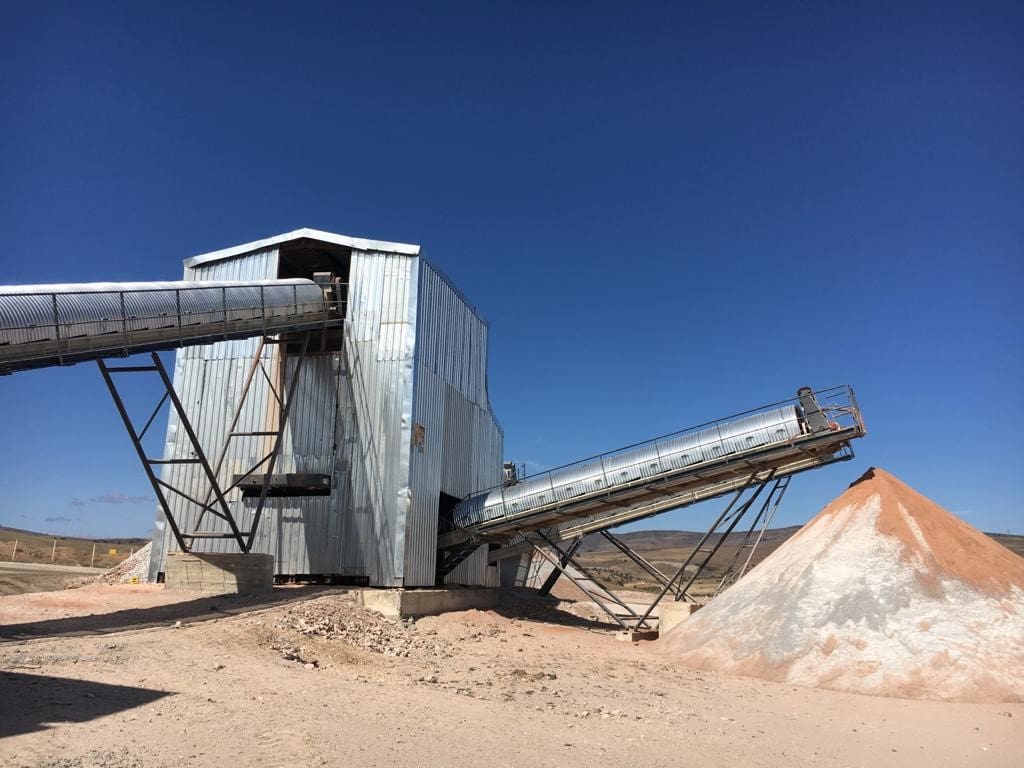
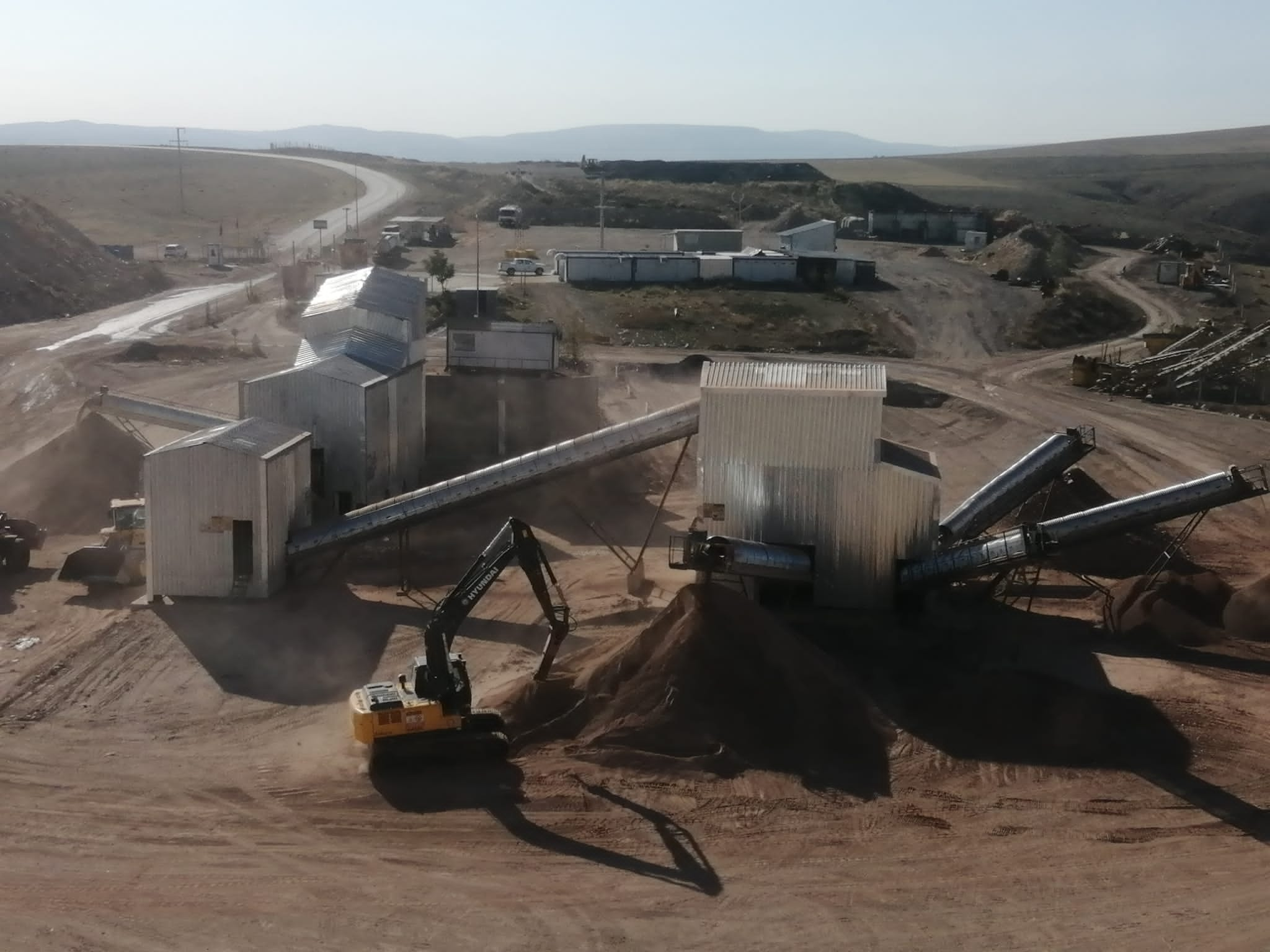
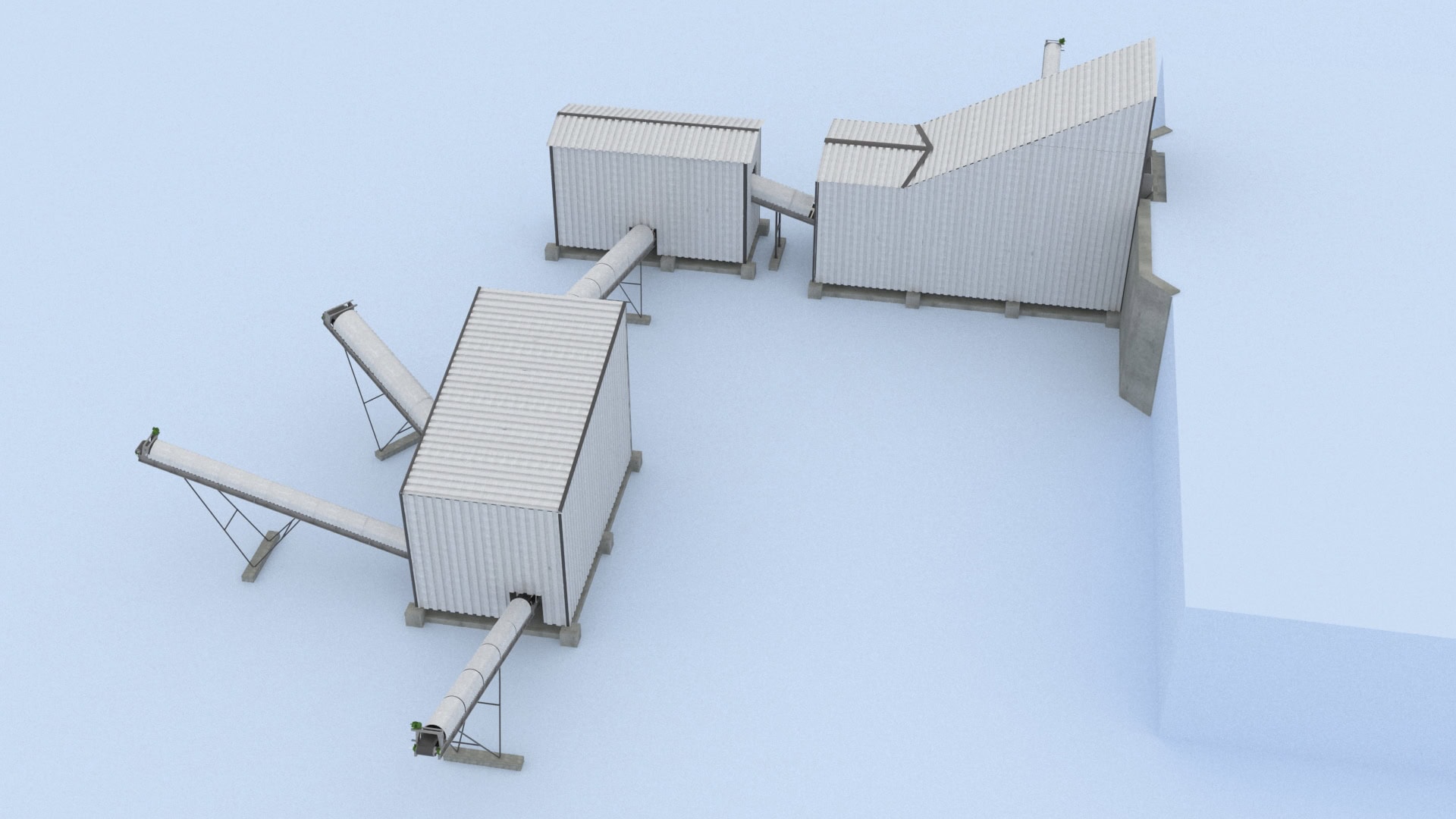
SMK series is selected as a mobile SMK1115 secondary crusher. The material crushed by the primary jaw crusher is directly fed to the secondary impact crushers, which have a high size reduction rate, and a cubic product is obtained. It is frequently used in crushing and screening plants and has low initial investment and operating costs. The material fed to SMK1115, which has a rotor size of Ø 1150 x 1500 mm, is impacted with the energy generated on the pallets as a result of the movement given to the rotor, and the material is crushed by hitting the crushing plates. In the first crushing stage, the material is reduced enough to pass through the distance between the pallets and the grinders. In the second and third crushing stages, the material is reduced to small enough dimensions to pass through the distance between the rotor pallets and the jaw mechanism and passes into the discharge chute. The pallets of the crushers in the SMK series can be used upside down.
In the plant, the UME series 2000 x 6000 mm 3-layer vibrating screen crushed material is classified into 5 mm, 15 mm and 25 mm product sizes. Vibrating screens are equipment that performs the sieving process, used to separate or classify materials of different sizes. The fed material, which is broken by SMK1115, moves forward at a certain speed thanks to vibration and is evenly distributed on the sieve surface. Materials smaller than the sieve size pass through the sieve eye openings and fall to the lower floor and are thus separated according to their size. By means of gutters, the material on each floor is taken separately. In the established facility, the return of the sieve was not fed to the secondary impact crusher and 4 different products were obtained. Depending on the characteristics of the material to be screened and the desired product dimensions, the sieve wires and the sieve coefficient vary. UME series vibrating screens provide practical screen wire replacement thanks to their front grooves with rail system.
The machines and conveyors in the mobile crushing and screening plantwere covered to prevent dust egress and a dust reduction system was added. A magnet is placed to separate the foreign metal parts and objects in the material that will pass over the belt conveyor at the exit of the primary crusher, a metal detector is placed to stop the belt conveyor by detecting and giving a warning, and a magnetic separator is placed to remove it from the system.