The crusher plant is fed by the UMG04 Rock Feeding Unit, which includes a 40 m³ feeding hopper and a 1350×5000 mm vibrating feeder. To ensure the separation of material before it enters the primary crusher, a two-stage 1400 mm wobbler feeder (6-bar and 5-bar) is installed, preventing clogging issues commonly encountered with grizzly screens. The wobbler feeder moves the material using synchronized eccentric shafts and elliptical parts, separating soil and fine material through rotation and gravity, ensuring cleaner and more consistent feeding to the primary crusher.
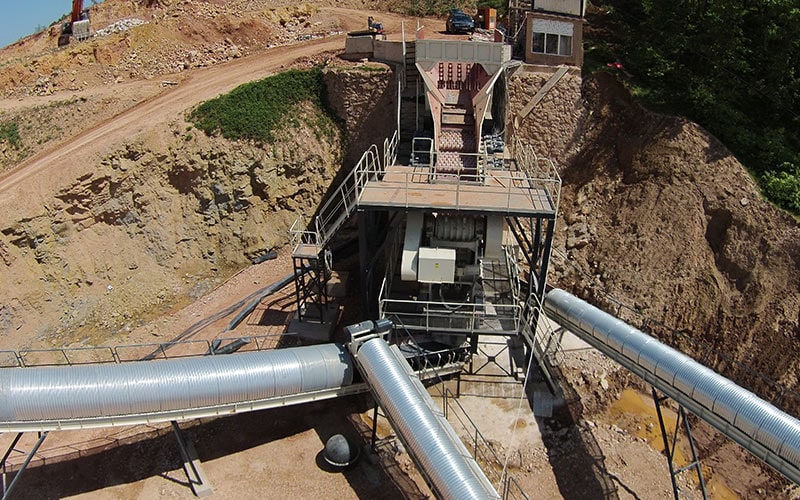
The primary crushing stage utilizes the UMK140 Jaw Crusher with a feed opening of 1370×1000 mm, which crushes the material between the fixed and moving jaws to achieve the desired size. The crushed material is then fed to the SMK1317 Secondary Impact Crusher, featuring a rotor size of Ø1280×1750 mm, known for its high reduction ratio and ability to produce cubic-shaped material. The material from the secondary crusher is sent to the existing vibrating screen for classification.
The sized material from the vibrating screen, along with the output from the UDK900 Vertical Shaft Impact Crusher (rotor diameter: Ø900 mm) and the tertiary crusher, is combined and sent to the UME2470 twin vibrating screens (2400×7000 mm, 4 decks). The return material from the UME2470 screens can either be fed back to the tertiary crusher or taken as product, while intermediate material is directed to the UDK900 Vertical Shaft Impact Crusher to enhance the cubic shape of the final product. The UME2470 screens produce three additional products, which are stored in the existing stock bunkers.
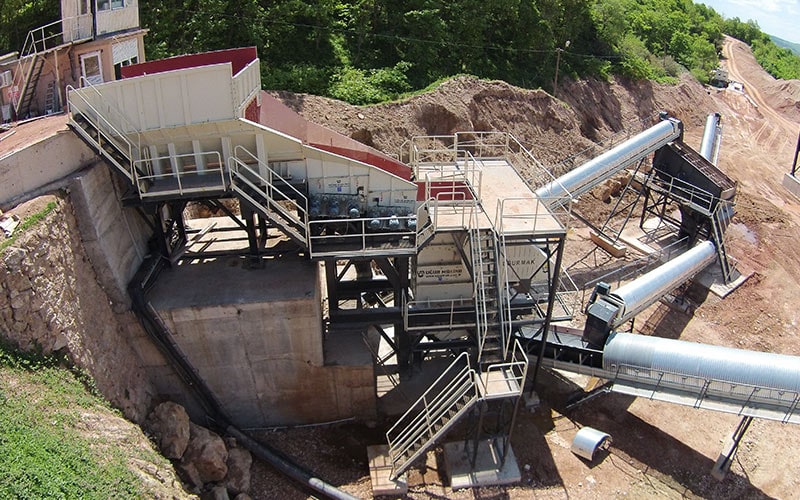
The plant’s conveyor belts are equipped with covers and walking platforms for safety and operational efficiency.
Key Features of the Plant:
– UMG04 Rock Feeding Unit with a 40 m³ hopper and 1350×5000 mm vibrating feeder.
– Two-stage 1400 mm wobbler feeder for material separation and clogging prevention.
– UMK140 Jaw Crusher for primary crushing.
– SMK1317 Secondary Impact Crusher for high reduction and cubic-shaped output.
– UDK900 Vertical Shaft Impact Crusher for fine and cubic material production.
– UME2470 twin vibrating screens (2400×7000 mm, 4 decks) for precise material classification.
– Covered conveyor belts with walking platforms for safety.
This advanced setup ensures efficient and high-quality dolomite processing, delivering a range of final products tailored to customer requirements.