The capacity of our stationary crushing and screening plant, which was established and put into operation in Hatay in 2023, is 500 tons/hour and the fed material is limestone. In the facility, the final product works smoothly in 5, 12, 19, 38 mm dimensions and with a capacity of 500 tons per hour and serves the aggregate needs of the region. Limestone (limestone) is a type of rock that is generally white, cream-toned, soft and sensitive to abrasion, contains a large amount of calcium carbonate (CaCO3) and is used in many areas such as construction, asphalt, concrete, filling material.
UMG04 rock feeding unit, one of the UĞURMAK brand UMG series vibrating grate feeders, was used in the facility. They undertake the task of feeding the jaw or impact crushers used in the primary stage. Offering high performance even under the most severe conditions, the UMG series feeders can be used for materials of all sizes, from blasted large materials to small stream materials. UMG04 consists of a feeding hopper with a volume of 40 m3 from which the material is fed, a vibrating feeder and a grid system on the feeder body. The feeding bunker is the bunker where the main feeding is made in a structure that offers high strength. It can be used in all mobile and fixed primary units. In vibrating feeders, the mechanical oscillation movement is created by two vibromotors with the same feature, and each oscillating movement gives movement to the fed material and allows it to move on the feeder. The purpose of the grid system is to bypass the material that does not need to enter the crusher instead of feeding it to the crusher, and to use the crusher with higher efficiency. This is the biggest reason why UMG series vibrating grid feeders are preferred especially in the primary stage. Thanks to the adjustable grid distance, the size of the product to be bypassed can be changed.
The product, which is by-passed in the grate feeder, is fed to the 2-layer sieve UME1650 UĞURMAK UME series, separating the material under the sieve, and ensuring that the material remaining on the sieve is delivered to the other stages of the system by skipping this stage without entering the crusher. Its purpose is to prevent unnecessary material from going to the crusher and to ensure that only the material of the desired size is processed.
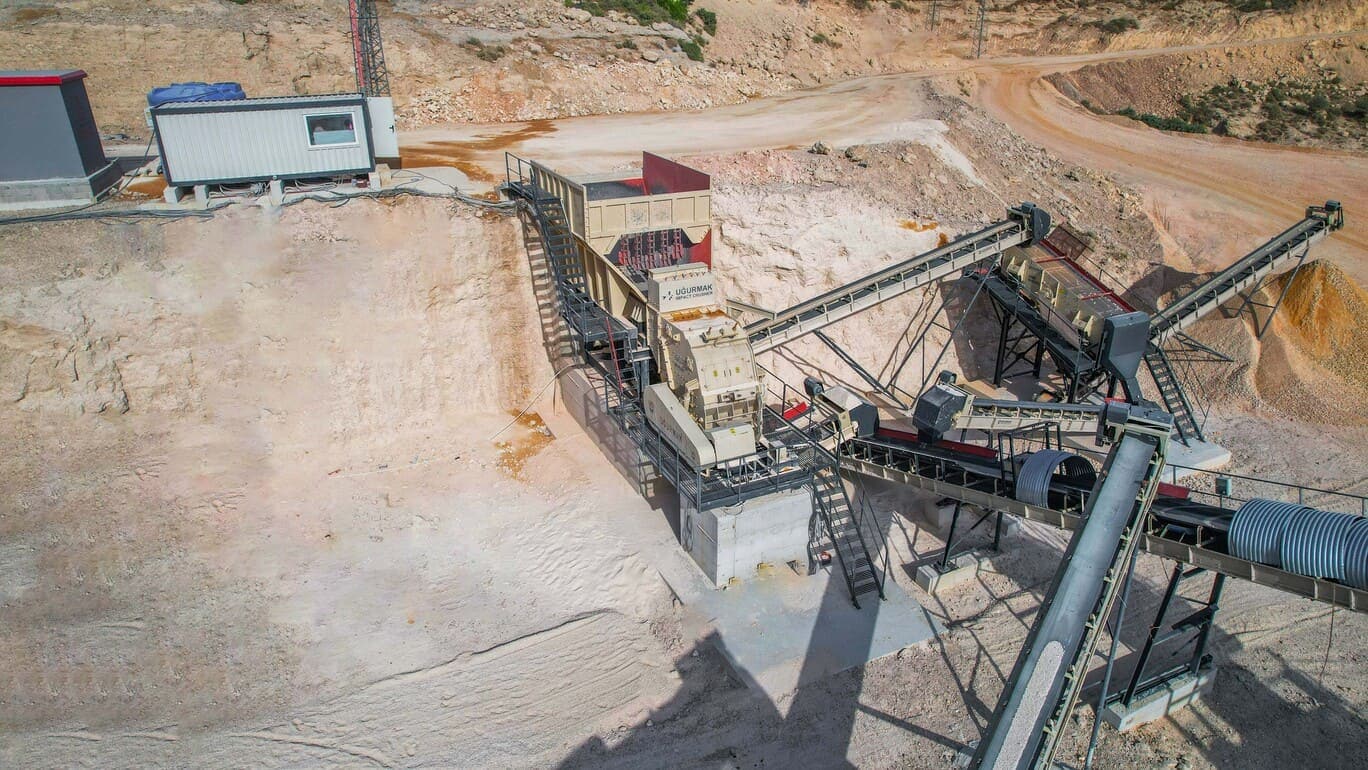
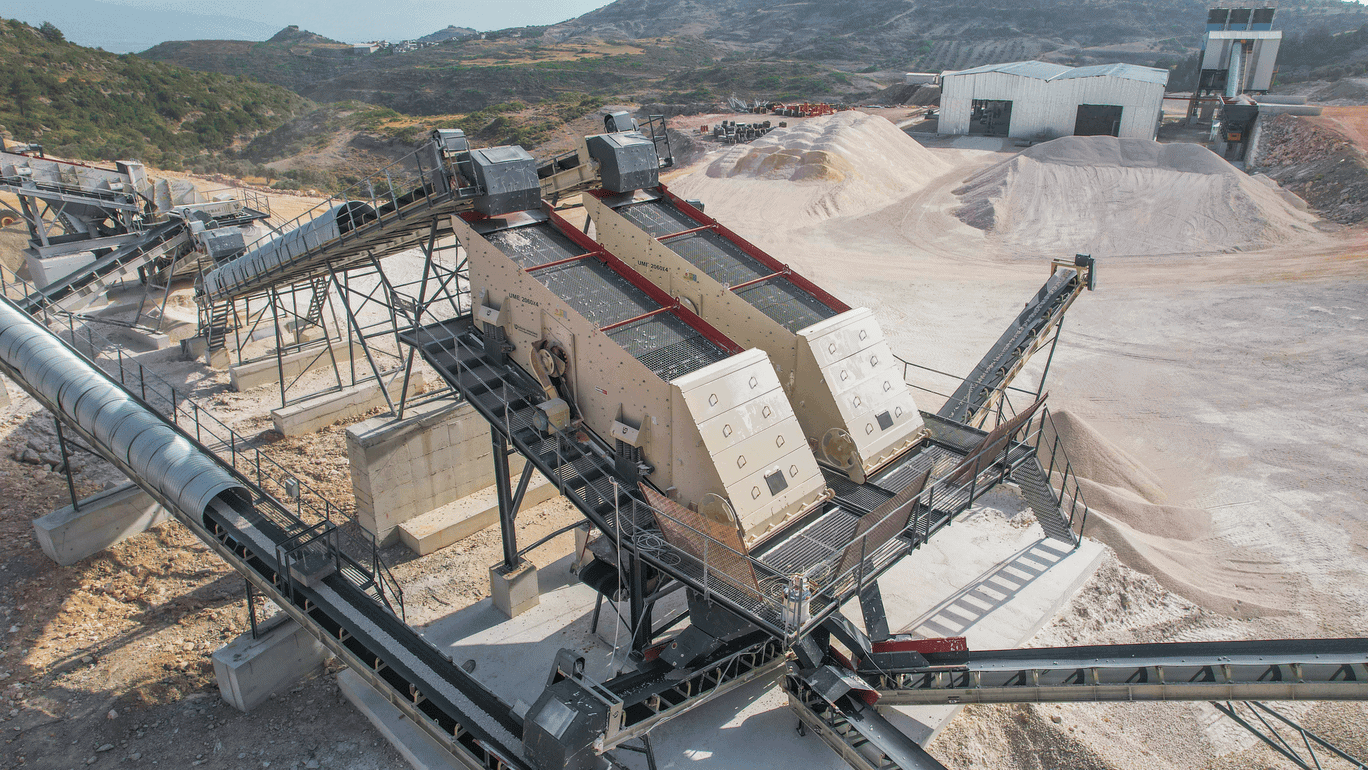
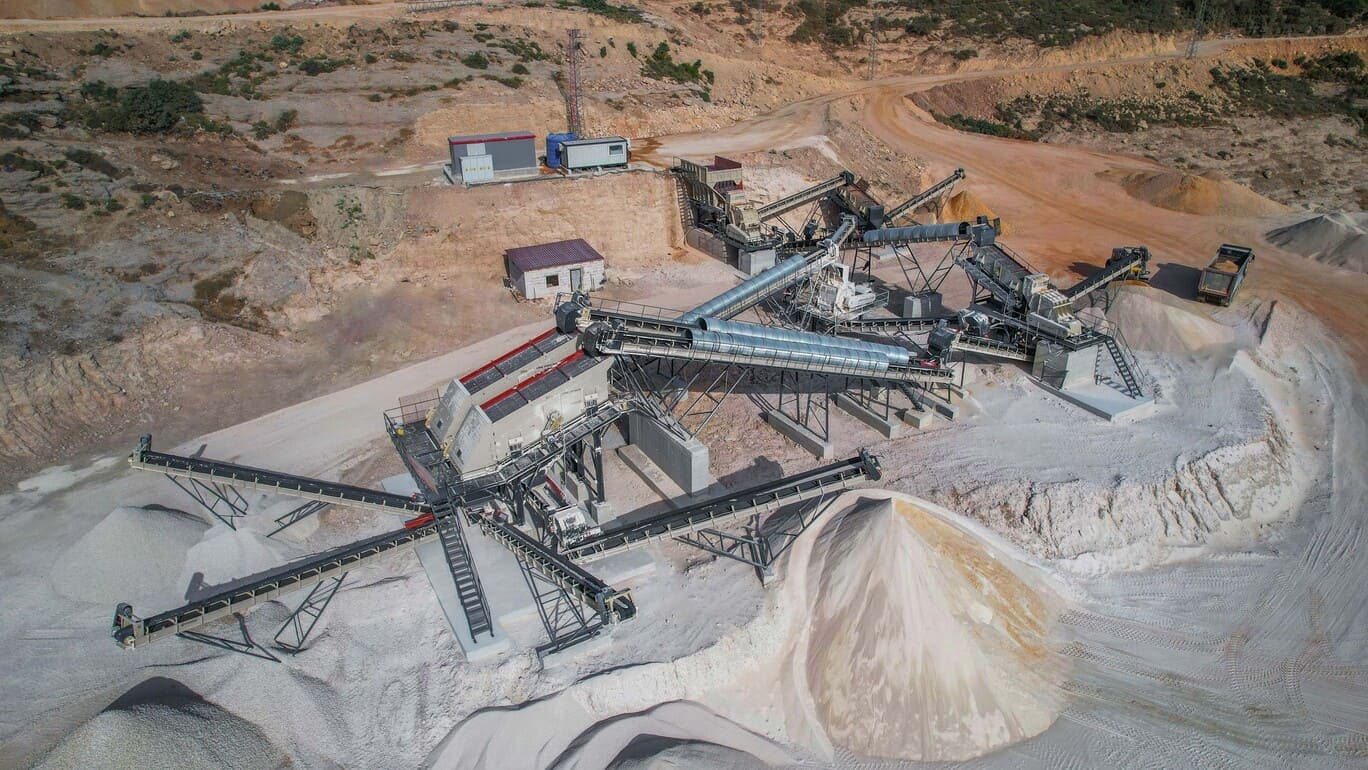
Primary impact crushers from our CDK series CDK1415 were used as primary crushers in the facility. UĞURMAK CDK series primary impact crushers work in harmony with the rotor, two pendulum systems and wear plates, providing very high size reduction rates in the crushing of very hard and non-abrasive materials. In this way, UĞURMAK CDK series primary impact crushers for limestone provide the most ideal crushing solution with high performance, continuous working capacity and low operating costs. These crushers, which consume less energy, provide advantages in construction and concrete production by shrinking large stones and giving products in a cubic structure.
The material coming out of the prime crusher is fed to the UME1650 2-layer sieve, allowing the material of the desired size to be taken as a product without entering the secondary crusher. Thus, material of a certain size can be separated from the system and taken as a product, and it prevents unnecessary material from entering the secondary impact crusher, allowing the crusher to work more efficiently.
UĞURMAK brand SMK series secondary impact crusher was used SMK1115 secondary crusher. Thanks to the secondary impact crushers, which are generally preferred as secondary crushers, the limestone coming from the primary impact crusher is reduced to the size of asphalt and concrete aggregate. Secondary crusher: It provides high reduction rate by making impact and gradual crushing with adjustable impact plates. Initial investment and operating costs are lower than other crusher types. For these reasons, UĞURMAK brand SMK series secondary impact crusher is the most preferred secondary crusher type in crushing and screening plants.
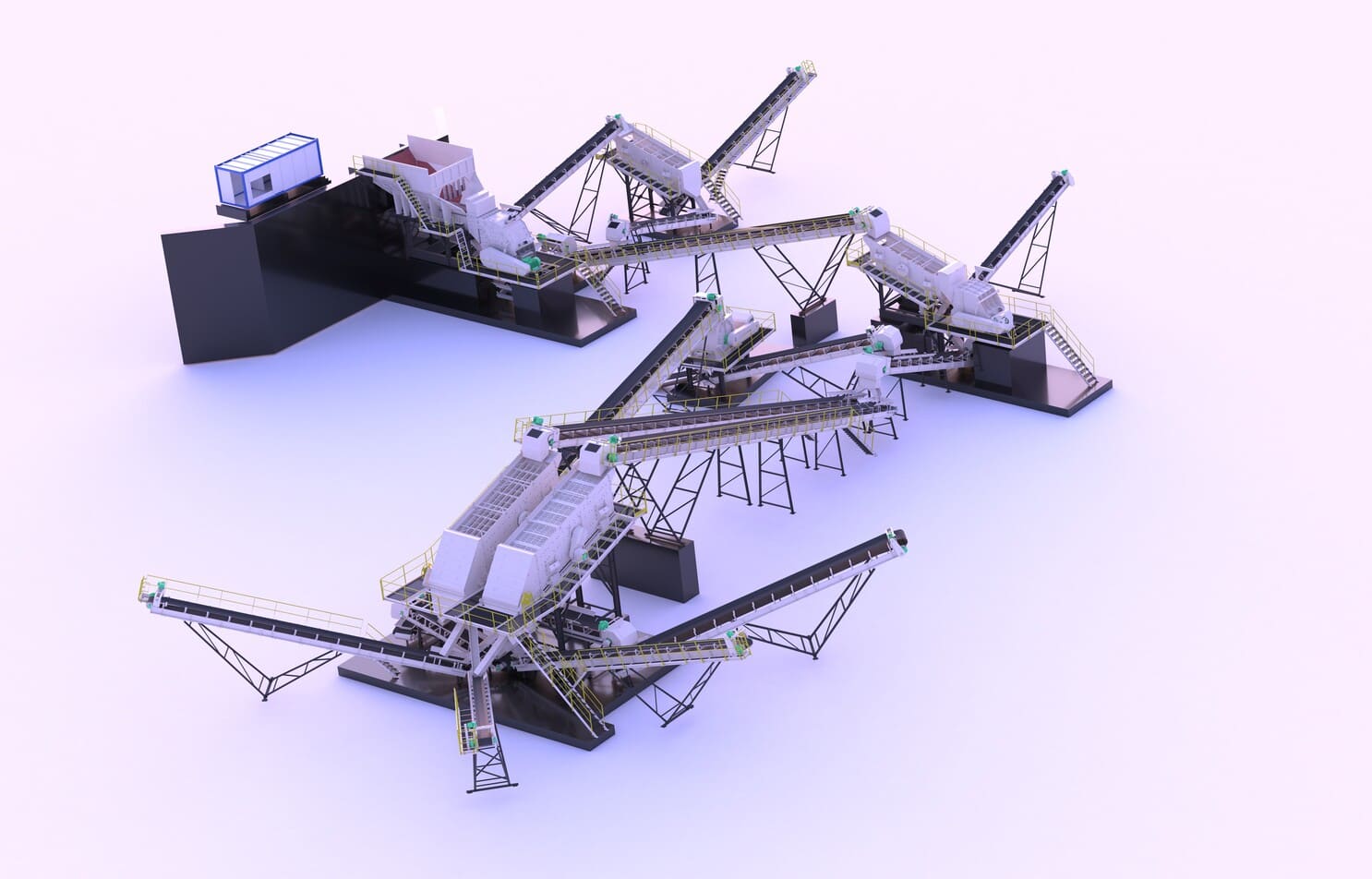
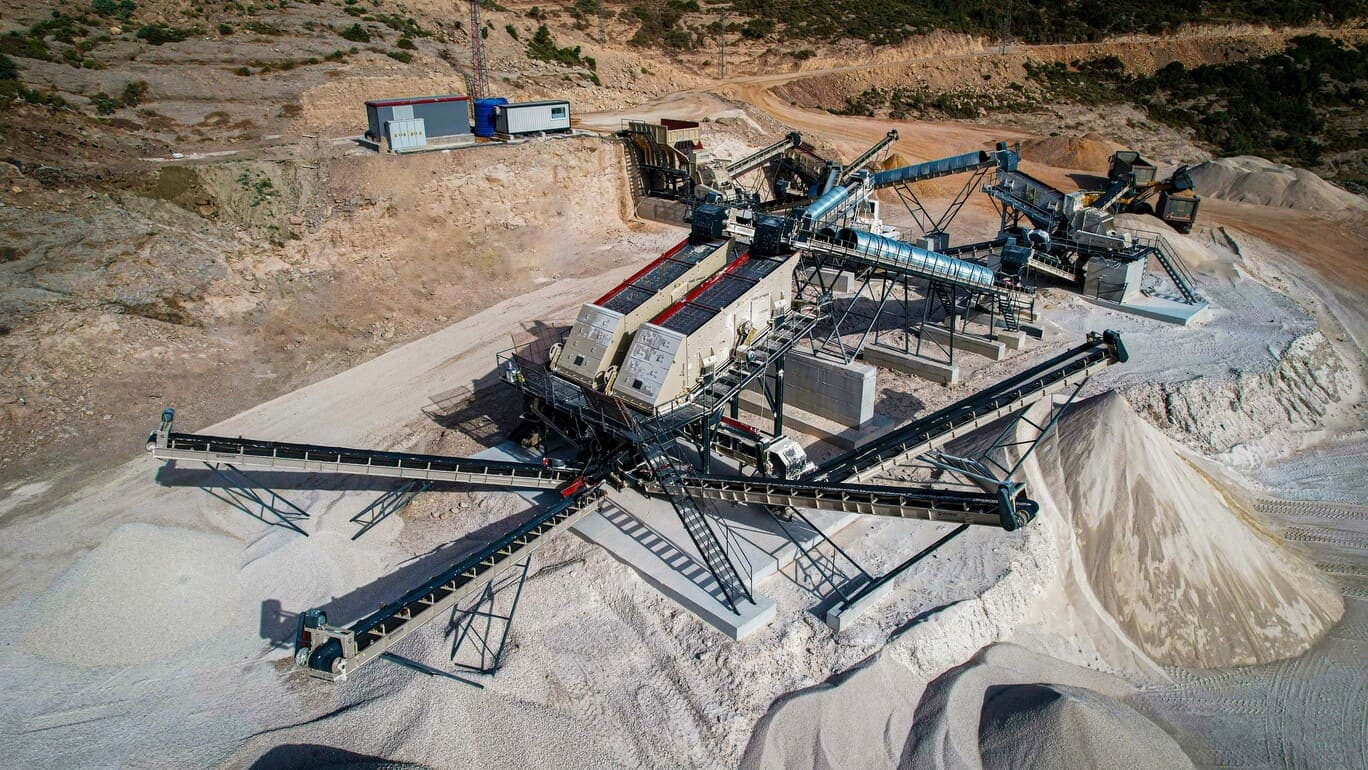
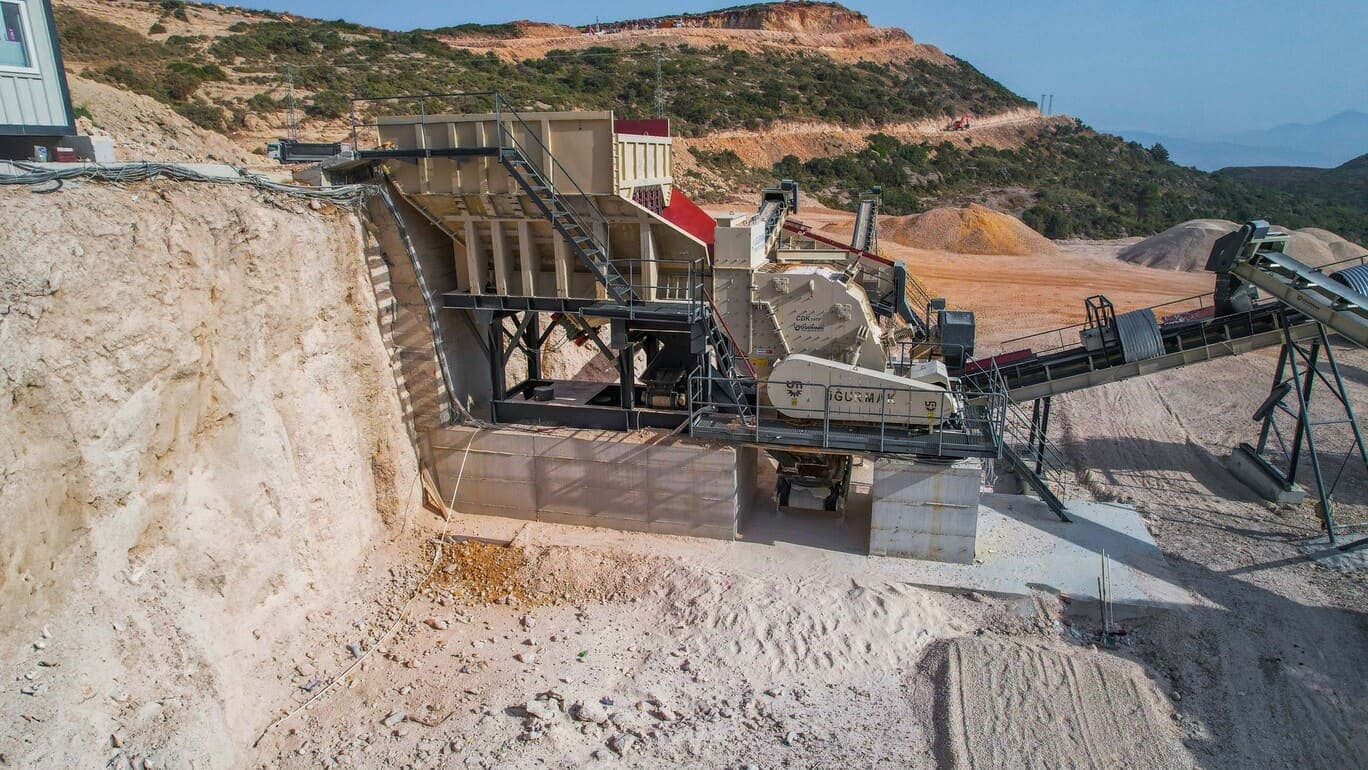
UĞURMAK UME series UME2060 for product sizing in the facility is carried out with two 4-layer sieves. These screens play an important role in the efficient operation of crushing and screening plants and the quality of the final product by providing the dimensioning of crushed material of different sizes. The material from the secondary and tertiary crusher is fed into the sieves, and the remaining material on the sieve is sent to the tertiary crusher, while the remaining material is classified into desired dimensions and taken as the final product. UME series inclined screens, with their weldless body design, have a more reliable body structure against the negative effects of vibration movement. In addition, the front groove has a rail system, so wire change can be done easily and quickly. The fact that the sieve body has platforms on all four sides provides safe and easy maintenance.
Tertiary impact crusher UTK1115 from our UTK series was used as a tertiary crusher in the facility. A high-speed rotating rotor with pallets placed on it applies a direct impact to the material, making it much thinner. The material that comes out of the secondary crusher and is fed to the screening system and remains on the sieve is fed to the tertiary crusher and the tertiary crushing process is carried out in the crushing and screening plant. The material fed to the tertiary crusher is fed to the secondary crusher outlet and included in the screening system again. Tertiary crusher is especially preferred for quality products used in fine aggregate production, concrete and asphalt construction. Since it has a symmetrical design, the rotor can rotate in both directions. The fact that the direction of rotation is two-way allows products to be taken in two different gradations without the need for adjustment changes. In addition, it ensures a longer life as there will be bidirectional wear on the rotor pallets. Thus, maintenance and operating costs are low.
There are a total of 2 magnet and metal detectors on the belt conveyors in the secondary crusher and tertiary crusher feed. The magnet is used to separate foreign metal parts and objects in the material, and the metal detector is used to detect these parts and objects and give a warning and stop the belt conveyor.
Machines used in the facility,
UMG04 Rock Feeding Unit
UME1650*2 Inclined Screen
CDK1415 Primary Impact Crusher
UME1650*2 Inclined Screen
SMK1115 Secondary Impact Crusher
UME2060*4 Inclined Sieve- 2 Pieces
UTK1115 Tertiary Impact Crusher
Type of Stone: Limestone
Capacity: 500t/h
Output: 5 mm, 12 mm, 29 mm, 38 mm