Our fixed crushing and screening plant, commissioned in Mardin in 2021, processes basalt material with a capacity of 200-250 tons per hour. The plant features state-of-the-art equipment from UĞURMAK, ensuring high efficiency and superior product quality.
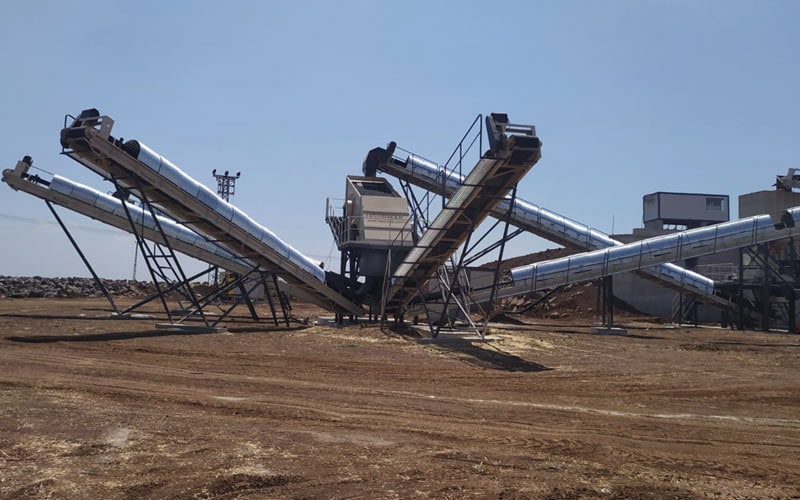
The UMG02 Rock Feeding Unit, part of the UMG series, is used for feeding the system. This unit includes a 30 m³ hopper and a 1200×5000 mm vibrating feeder, designed to feed primary crushers such as jaw or impact crushers. Its adjustable grizzly spacing allows for flexibility in bypassing oversized material. The primary crushing stage utilizes the UMK110 Jaw Crusher with a feed opening of 1100×850 mm. To prevent unnecessary material from entering the primary crusher, a UME1240 2-deck inclined screen is used as a bypass screen, ensuring only the desired material size is processed.
Material from the primary crushing stage is fed to a cone crusher, which serves as the secondary crusher. The cone crusher refines the material, ensuring uniformity in size and optimal results. The UME2060 2-deck inclined screen classifies the material, with +40 mm material sent back to the cone crusher for further crushing and -40 mm material directed to the UDK900 Vertical Shaft Impact Crusher. The UDK900, with a rotor diameter of Ø900 mm, is ideal for producing fine, cubic-shaped material due to its high-speed rotor and impact crushing principle.
The plant includes two UMVB sand feeding hoppers (20 m³ and 10 m³), which ensure continuous and consistent feeding of the cone crusher and vertical shaft impact crusher. These hoppers are equipped with vibrating feeders at their outlets.
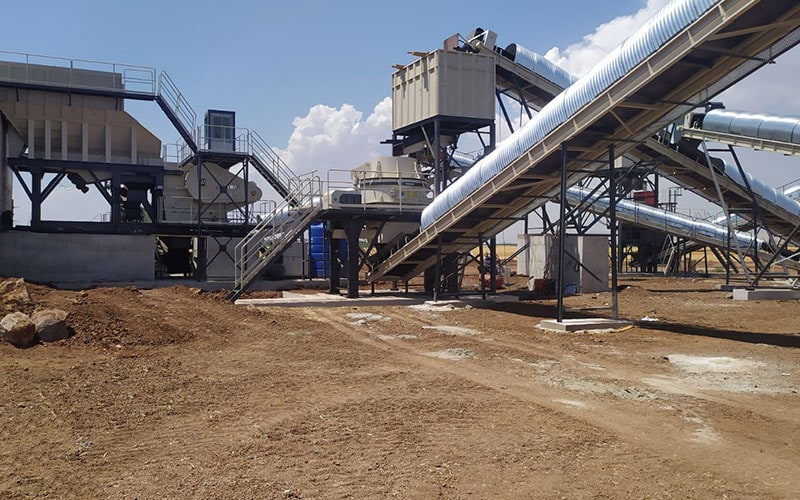
The UME2060 4-deck inclined screen plays a crucial role in sizing the crushed material into different fractions, ensuring efficient operation and high-quality final products. Material from the vertical shaft impact crusher is classified into specific sizes, with oversized material returned to the crusher and the remaining material sorted into final products. The final product sizes obtained are 5 mm, 12 mm, 19 mm, and 25 mm.
To protect the equipment, the conveyor belts feeding the cone crusher and vertical shaft impact crusher are equipped with magnets and metal detectors. The magnets separate foreign metal objects from the material, while the metal detectors detect such objects and stop the conveyor belts to prevent damage.
Material Type: Basalt
Capacity: 200-250 tons/hour
Final Products: 5 mm, 12 mm, 19 mm, 25 mm
Equipment Used in the Plant:
– UMG02 Rock Feeding Unit
– UMK110 Primary Jaw Crusher
– UME1240*2 Inclined Screen
– UMVB 20 m³ Sand Feeding Hopper
– Cone Crusher
– UME2060*2 Inclined Screen
– UMVB 10 m³ Sand Feeding Hopper
– UDK900K Vertical Shaft Impact Crusher
– UME2060*4 Inclined Screen
This advanced setup ensures efficient and reliable basalt processing, delivering high-quality final products tailored to customer needs.